Table Content
1. Introduction |
6. Comparison with Other Substrates - Alumina vs. FR-4 substrates - Alumina vs. ceramic substrates |
2. Properties of Alumina Substrates - Thermal conductivity - Electrical insulation - Mechanical strength |
7. Challenges and Limitations - Cost considerations - Surface finishes and Bonding techniques |
3. Manufacturing Process - Raw materials - Forming methods - Firing process |
8. Future Trends - Miniaturization and high-density packaging - Integration with advanced technologies |
4. Applications of Alumina Substrates - Printed circuit boards (PCBs) - Power electronic devices - LED packaging |
9. Conclusion |
5. Advantages of Alumina Substrates - High temperature resistance - Excellent electrical properties - Reliability and durability |
10. FAQs
- What is the difference between alumina substrates and ceramic substrates? - Can alumina substrates be used in high-power applications? - Are alumina substrates environmentally friendly? - How are alumina substrates manufactured? - What is the typical thickness of alumina substrates? |
Introduction
The electronics industry constantly demands materials with exceptional properties to meet the ever-increasing technological advancements. Alumina substrates, also known as aluminum oxide substrates, have emerged as a crucial component in various electronic devices and systems. This article aims to explore the characteristics of alumina substrates, their manufacturing process, applications, advantages, as well as their role in shaping the future of the electronics industry.
Properties of Alumina Substrates
Alumina substrates possess several key properties that make them highly suitable for electronic applications.
Thermal conductivity
Firstly, these substrates exhibit excellent thermal conductivity, ensuring efficient heat dissipation in electronic devices. This property helps in preventing overheating, which is vital for maintaining optimal performance and prolonging the lifespan of electronic components.
Electrical insulation
Secondly, alumina substrates offer exceptional electrical insulation, enabling effective isolation between different circuit elements. This insulation property is crucial for preventing short circuits and ensuring reliable and safe operation.
Mechanical strength
Lastly, alumina substrates demonstrate impressive mechanical strength, providing durability and resistance to mechanical stress, vibrations, and shocks.
Manufacturing Process
The manufacturing process of alumina substrates involves several stages.
Raw materials
It begins with the selection of high-purity raw materials, such as aluminum hydroxide or aluminum oxide powder. These materials are carefully mixed and blended to achieve the desired composition and consistency.
Forming methods
Next, the mixture is formed into a green sheet using various techniques like tape casting or extrusion. The green sheets are then cut into the desired shape and size.
Firing process
The formed substrates undergo a firing process, typically carried out at high temperatures, to sinter and densify the material. This firing process helps in achieving the required mechanical strength and electrical properties.
Applications of Alumina Substrates
Alumina substrates find extensive use in various electronic applications.
Printed circuit boards (PCBs)
One of the primary applications is in the manufacturing of printed circuit boards (PCBs). Alumina substrates provide a stable and reliable platform for mounting electronic components and creating complex circuits.
Power electronic devices
These substrates are also widely used in power electronic devices, such as power modules and inverters, due to their excellent thermal conductivity and electrical insulation properties.
LED packaging
Furthermore, alumina substrates are employed in LED packaging, where their high thermal conductivity helps in dissipating the heat generated by LEDs, improving their performance and lifespan.
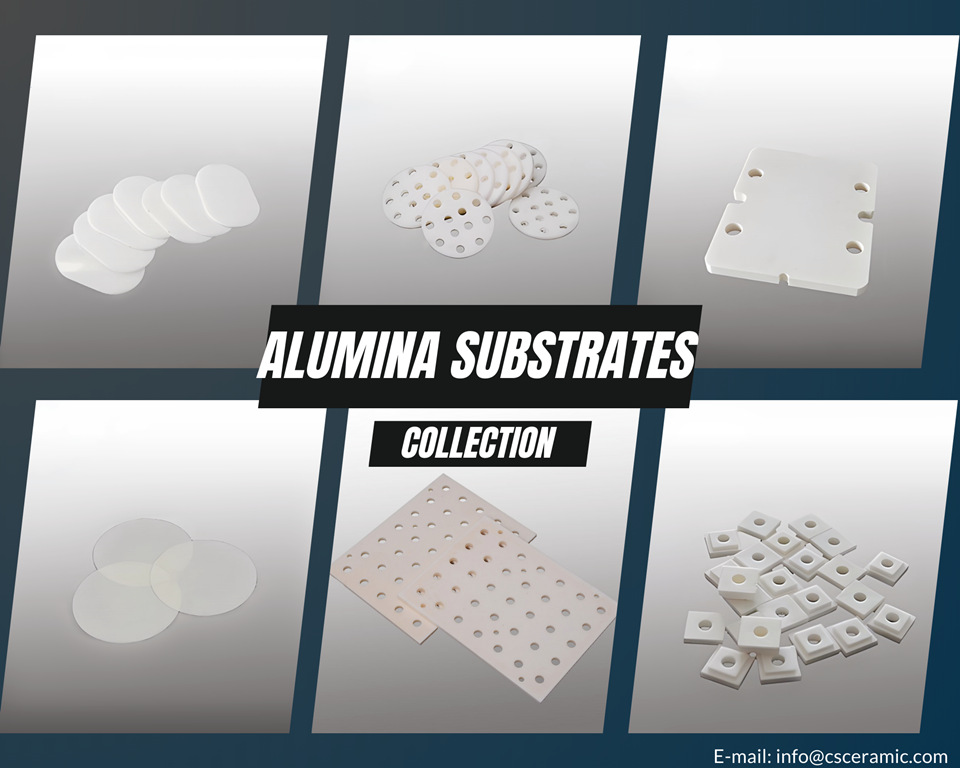
Advantages of Alumina Substrates
The utilization of alumina substrates offers several advantages in the electronics industry.
High temperature resistance
Firstly, their high temperature resistance allows electronic devices to operate in challenging environments without compromising performance.
Excellent electrical properties
Alumina substrates also exhibit excellent electrical properties, including low dielectric loss and high breakdown voltage, ensuring reliable operation even at high frequencies.
Reliability and durability
Moreover, these substrates offer long-term reliability and durability, making them suitable for demanding applications where stability is crucial.
Comparison with Other Substrates
Aluminum oxide substrates vs. FR-4 substrates
When comparing alumina substrates with other common substrates, two noteworthy comparisons arise: alumina substrates vs. FR-4 substrates and alumina substrates vs. ceramic substrates. Alumina substrates provide superior thermal conductivity, allowing better heat dissipation compared to FR-4 substrates, which are commonly used in consumer electronics. Additionally, alumina substrates offer higher electrical insulation properties than FR-4 substrates, making them suitable for high-voltage applications.
Aluminium oxide substrates vs. other ceramic substrates
Compared to ceramic substrates, alumina substrates exhibit better mechanical strength, enabling them to withstand mechanical stress and vibrations more effectively.
Challenges and Limitations
While alumina substrates offer significant advantages, there are certain challenges and limitations to consider.
Cost considerations
One of the primary concerns is the cost of alumina substrates, which can be higher compared to other substrates. This cost consideration should be evaluated against the specific requirements and benefits offered by alumina substrates.
Surface finishes and bonding techniques
Additionally, surface finishes and bonding techniques can pose challenges due to the high hardness and chemical inertness of alumina substrates. Specialized processes may be required to achieve reliable bonding and create compatible surface finishes.
Future Trends
Miniaturization and high-density packaging
In line with the growing demand for miniaturization and high-density packaging, alumina substrates are expected to play a vital role in the future of the electronics industry. These substrates provide a foundation for developing advanced technologies that require compact and efficient electronic systems.
Integration with advanced technologies
Integration with emerging technologies, such as 5G, Internet of Things (IoT), and electric vehicles, will further drive the demand for alumina substrates with enhanced performance and reliability.
Conclusion
Alumina substrates have become indispensable in the electronics industry, offering exceptional properties that contribute to the efficient and reliable operation of electronic devices and systems. Their thermal conductivity, electrical insulation, and mechanical strength make them highly suitable for various applications, including PCBs, power electronic devices, and LED packaging. Despite challenges and limitations, the advantages provided by alumina substrates position them as a key material for the future of electronics.
FAQs
Q1: What is the difference between alumina substrates and ceramic substrates?
A1: Alumina substrates are a type of ceramic substrate, specifically made from aluminum oxide. While all alumina substrates are ceramic substrates, not all ceramic substrates are alumina substrates. Alumina substrates offer superior mechanical strength compared to other ceramic substrates, making them more suitable for demanding applications in the electronics industry.
Q2: Can alumina substrates be used in high-power applications?
A2: Yes, alumina substrates are commonly used in high-power applications. Their excellent thermal conductivity and electrical insulation properties make them well-suited for power electronic devices that generate significant heat and require effective heat dissipation.
Q3: Are alumina substrates environmentally friendly?
A3: Alumina substrates are generally considered environmentally friendly. They are made from abundant raw materials and are non-toxic. However, it is important to ensure proper disposal and recycling practices to minimize any potential environmental impact.
Q4: How are alumina substrates manufactured?
A4: The manufacturing process of alumina substrates involves selecting high-purity raw materials, forming them into green sheets, cutting them into desired shapes, and firing them at high temperatures to achieve the required properties. The specific manufacturing techniques may vary, but they generally follow these fundamental steps.
Q5: What is the typical thickness of alumina substrates?
A5: The thickness of alumina substrates can vary depending on the specific application. However, typical thicknesses range from a few hundred micrometers to several millimeters, depending on the required mechanical strength and thermal performance.
Thank you for reading. We invite you to visit CSCERAMIC for more information if you would like to learn more about industrial ceramic material and the advanced range of ceramic products we offer.