Can Alumina Ceramic Crucibles be Used in Induction Heating Systems?
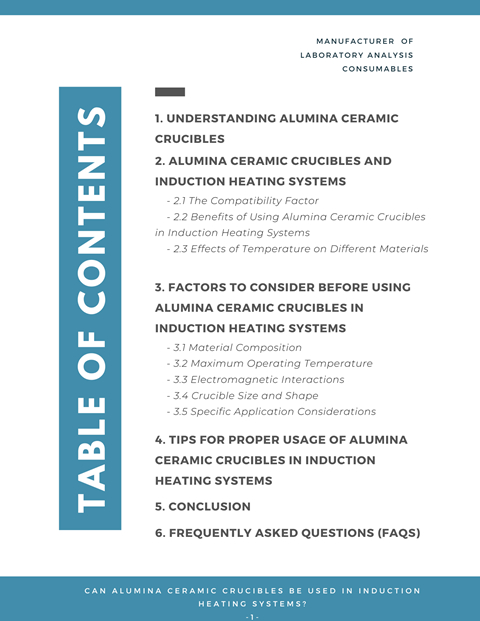
Alumina ceramic crucibles have emerged as a vital component in various industrial processes, particularly in high-temperature applications. One area where these crucibles have garnered significant attention is in induction heating systems. In this article, we will delve deeper into the relationship between alumina ceramic crucibles andinduction heating, the factors to consider before using them in such systems, and how temperature affects different materials during the process.
Understanding Alumina Ceramic Crucibles
Before exploring their application in induction heating systems, it is crucial to understand the unique properties of alumina ceramic crucibles. Composed primarily of aluminum oxide, these crucibles undergo a high-temperature manufacturing process that results in a dense, strong, and chemically resistant structure. As a result, they excel in demanding environments that involve extreme temperatures and corrosive substances.
Alumina Ceramic Crucibles and Induction Heating Systems
2.1 The Compatibility Factor
Induction heating systems have become widely adopted for their efficiency in melting, heat treating, and sintering materials. However, the compatibility of alumina ceramic crucibles with induction heating systems depends on several critical factors. One such factor is the interaction of electromagnetic fields generated during induction heating with the alumina crucible.
While alumina ceramic crucibles are ideal for high-temperature applications, their electromagnetic properties may affect their performance in induction heating. The crucibles' response to electromagnetic fields must be carefully evaluated to ensure they can withstand the induction process without compromising their structural integrity.
2.2 Benefits of Using Alumina Ceramic Crucibles in Induction Heating Systems
Despite the considerations for compatibility, the use of alumina ceramic crucibles in induction heating systems offers several significant advantages. Some of the key benefits include:
-
Thermal Shock Resistance
Alumina ceramic crucibles exhibit high thermal shock resistance, making them ideal for rapid heating and cooling cycles during induction processes.
-
Chemical Resistance
These crucibles demonstrate excellent chemical resistance, ensuring compatibility with a wide range of materials and substances.
-
Mechanical Strength
Alumina ceramic crucibles possess superior mechanical strength, reducing the risk of cracking or failure during handling and processing.
-
Low Porosity
The low porosity of these crucibles prevents contamination, ensuring the purity of the materials being processed.
-
Cost-effectiveness
With their extended lifespan and durability, alumina ceramic crucibles offer cost-effectiveness in the long run.
2.3 Effects of Temperature on Different Materials
Induction heating involves subjecting materials to high temperatures to achieve the desired outcomes. The behavior of materials under different temperature conditions is a critical consideration. Some materials may undergo phase changes, chemical reactions, or structural modifications when exposed to extreme heat. Understanding the effects of temperature on different materials is essential for successful induction heating processes using alumina ceramic crucibles.
Factors to Consider Before Using Alumina Ceramic Crucibles in Induction Heating Systems
3.1 Material Composition
The material composition of the substance to be heated is a critical factor to consider when using alumina ceramic crucibles in induction heating systems. Different materials may interact differently with alumina ceramic crucibles at high temperatures, potentially affecting both the material and the crucible itself.
Some materials may exhibit chemical reactions with alumina, leading to contamination or degradation of the crucible. It is essential to thoroughly analyze the compatibility of the material with the crucible before commencing the induction heating process. Manufacturers and researchers should consult material compatibility charts and conduct thorough tests to ensure the safe and efficient use of alumina ceramic crucibles for specific materials.
3.2 Maximum Operating Temperature
Induction heating systems can reach extremely high temperatures, depending on the application. Before using alumina ceramic crucibles, it is crucial to determine the maximum operating temperature of the induction system and ensure that the crucible can withstand these temperatures without compromising its structural integrity.
Alumina ceramic crucibles are known for their exceptional thermal stability and can withstand temperatures up to thousands of degrees Celsius. However, it is essential to verify the specific temperature limits of the chosen crucible and avoid subjecting it to temperatures beyond its rated capacity. Exceeding the maximum operating temperature may lead to crucible failure, resulting in material loss and potential damage to the induction heating system.
3.3 Electromagnetic Interactions
Induction heating relies on electromagnetic fields to generate heat within the material being processed. As alumina ceramic crucibles are electrically insulating materials, they may interact with the electromagnetic fields during induction heating.
To minimize electromagnetic interactions, proper insulation measures are necessary. Refractory materials, such as boron nitride, can be used as a barrier between the alumina crucible and the inductor coil. These materials help reduce the influence of electromagnetic fields on the crucible, ensuring its stability and preventing undesirable effects on the induction heating process.
3.4 Crucible Size and Shape
The size and shape of the alumina ceramic crucible significantly impact the efficiency and uniformity of induction heating. Crucible size should be chosen carefully, considering the amount of material to be processed and the available induction heating equipment.
A larger crucible may be suitable for batch processing, allowing for the simultaneous heating of a larger quantity of material. On the other hand, smaller crucibles are ideal for experiments or processes with limited material quantities, ensuring better temperature control and uniformity.
The shape of the crucible also plays a role in heat distribution. Crucibles with wider bases and lower heights promote even heating, preventing temperature gradients and minimizing the risk of material non-uniformity during induction heating.
3.5 Specific Application Considerations
Before employing alumina ceramic crucibles in induction heating systems, it is vital to take into account the specific application requirements. Different applications may demand unique crucible properties, such as thermal conductivity, chemical resistance, and purity.
For example, applications involving aggressive chemical reactions may necessitate the use of high-purity alumina ceramic crucibles to prevent contamination. In contrast, high-temperature processes might require crucibles with excellent thermal stability.
Researchers and engineers must carefully evaluate the specific needs of the application and choose the most appropriate alumina ceramic crucible accordingly. Properly matching the crucible's properties to the application ensures optimal performance, efficiency, and safety during induction heating processes.
Tips for Proper Usage of Alumina Ceramic Crucibles in Induction Heating Systems
The proper usage of alumina ceramic crucibles in induction heating systems is crucial to ensure their longevity and optimal performance. Let's further detail the key tips for using these crucibles effectively:
Gradual Preheating
Preheating the alumina ceramic crucible gradually is essential to prevent thermal shock. Rapid and extreme temperature changes can cause stress within the crucible, leading to cracking or failure. Gradual preheating allows the crucible to expand uniformly, reducing the risk of damage.
Avoid Sudden Temperature Changes
Similarly, during the heating and cooling process, sudden and drastic temperature changes should be avoided. Alumina ceramic crucibles exhibit excellent thermal shock resistance, but they are not immune to rapid temperature fluctuations. A gradual approach ensures the crucible's structural integrity remains intact.
Use Refractory Materials
To minimize electromagnetic interactions with the crucible, it is advisable to use refractory materials as insulating layers. Placing appropriate refractory materials between the alumina crucible and the inductor coil acts as a buffer, reducing the influence of electromagnetic fields on the crucible and enhancing its stability.
Handle with Care
Alumina ceramic crucibles are sturdy but require careful handling during loading and unloading processes. Mishandling can lead to cracks or damage to the crucible, compromising its performance and longevity. Using proper tools and exercising caution while handling the crucible is essential.
Regular Cleaning and Maintenance
Regular cleaning and maintenance are crucial to extend the lifespan of alumina ceramic crucibles and preserve their performance. After each use, remove any remaining solid residues gently. Regularly inspect the crucible for signs of wear or damage. Cleaning with mild detergent and rinsing thoroughly will prevent contamination and ensure the crucible's purity for future use.
By following these usage tips and considering the specific factors discussed earlier, industries and researchers can make the most of alumina ceramic crucibles in their induction heating processes. These crucibles' outstanding properties contribute to efficient and successful high-temperature applications, fostering advancements in various industrial fields.
Conclusion
Alumina ceramic crucibles have proven to be valuable assets in induction heating systems. Their exceptional thermal shock resistance, chemical resistance, and mechanical strength make them an ideal choice for high-temperature applications. However, ensuring their compatibility with specific induction heating processes requires careful consideration of various factors, including material composition, temperature effects, and electromagnetic interactions. By understanding these aspects and following proper usage guidelines, industries can optimize their induction heating processes and benefit from the superior performance of alumina ceramic crucibles.
Frequently Asked Questions (FAQs)
1. Can alumina ceramic crucibles be used for metal melting applications?
Yes, alumina ceramic crucibles can be used for metal melting applications, especially for non-ferrous metals.
2. Are alumina ceramic crucibles compatible with acidic substances?
Yes, alumina ceramic crucibles exhibit excellent chemical resistance, making them compatible with acidic substances.
3. How do alumina ceramic crucibles compare to graphite crucibles in terms of performance?
Alumina ceramic crucibles offer better thermal shock resistance and chemical stability compared to graphite crucibles.
4. Can alumina ceramic crucibles be reused after a material has been processed in them?
Yes, alumina ceramic crucibles can be reused after proper cleaning and inspection.
5. What is the typical lifespan of an alumina ceramic crucible in an induction heating system?
The lifespan of an alumina ceramic crucible depends on various factors but can range from several months to years with proper care.
Thank you for reading. We invite you to visit CSCERAMIC for more information if you would like to learn more about industrial ceramic material and the advanced range of ceramic products we offer.