Zirconia ceramic is a kind of new ceramic material with white color, when contain some impurities it would be yellow or gray. It is widely used in various industries for its features of broken resistance, wear resistance, high hardness, high-temperature resistance, superior corrosion resistance, no rust, insulation and oil-free self-lubrication. In this article, manufacturing procedures and machining processes of zirconia ceramics are briefly introduced.
- How to manufacture zirconia ceramic?
Step 1. Identifying zirconia powder, which is the raw material
For its physical properties, zirconia is white, amorphous, odorless and tasteless powder. And for its chemical properties, zirconia powder is soluble in sulfuric acid solution(the proportion of sulfuric acid to water is 2:1). It is soluble sparingly in hydrochloric acid and nitric acid and it is soluble slowly in hydrofluoric acid, but it is insoluble in water. Its density is 5.85g/cm3, melting point is 2680℃ and boiling point is 4300℃, hardness is second only to diamond.
Step 2. Forming methods of zirconia ceramic
Inject forming, dry press forming and isostatic press forming are the main forming methods of zirconia ceramics. Forming methods is selected according to the product shape, product quantity and product properties, which would bring a difference to the performance of product.
Step 3. Ceramic sintering
Ceramic sintering is a general term for the densification process and phenomenon of ceramic blanks under high temperature, sintering temperature of zirconia ceramic is 1450℃.
For sintering procedures, first heat up the furnace up to around 300℃, continue raise the temperature up to the highest temperature, and keep several hours. Then start to decrease the temperature, until when the temperature is lower than 100℃, the products can be taken out from the furnace.
Step 4. Ceramic finish machining
This step refers to a series of fashioning operations, such as drilling, grinding, mirror polishing, etc.
Step 5. Quality Inspection
The last step is quality inspection for final product.
- What are the main machining processes of zirconia ceramic?
1.Grinding process
Zirconia ceramic is half finished after sintering, further grinding process is applied according to desired shapes.
As a new process method, the grinding process is applied under an electrolysis condition to manufacture zirconia ceramics. It is required to fix the metallic grinding wheels before adding electrolytic grinding fluid to electrode and grinding wheels and then turn on pulse current during grinding.
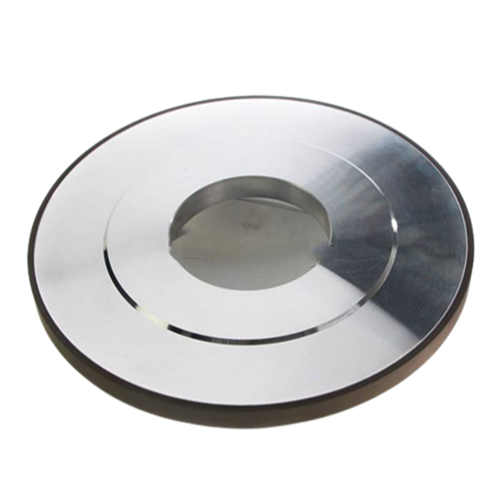
The sharpness of the grinding wheel is maintained throughout the whole process, which could ease the difficulty of fitting the wheels and guarantee the ultra-precision of grinding.
2.Polishing process
Polishing process is an essential procedure where a subtle removal on surface by using grinding medium can obtain ultra-precise effect.
The polishing process of zirconia ceramics refers to a procedure to apply fine treatment on the surface of workpieces. With the wide industrial application of zirconia ceramic polishing, different zirconia ceramic product has its individual polishing method and fundamental.
The polishing methods of zirconia ceramics mainly include flat surface polishing, cylindrical polishing, curved surface polishing and complex shaped workpieces polishing.
- Flat surface polishing is implemented by the effect between grinding wheels, grinding fluid and workpieces, applying the principle of chemical physics. Generally, the flatness can be up to 0.002mm and the roughness can be up to 0.000002mm after polishing.
- Cylindrical polishing is relatively hard to be implemented due to its operation being more automatic, therefore the accuracy of zirconia ceramic surface can only reach about 0.02mm.
- Curved surface polishing is operated by ultrasonic grinding machines, which is used for chamfering or other process, in order to obtain a flat and smooth surface effect.
- Considering the angles and uneven surface, the complex shaped workpieces polishing is hard to operate unless using tumbling barrel grinding machines and grinding them repetitively with grinding stones then a preferable surface effect can be obtained.
3. Plasticity process
Plasticity removal and brittleness removal are traditional plasticity processes. These two kinds of methods have their drawbacks that brittleness removal can be achieved completely but plasticity removal effect is slight.
To improve the effect of plasticity removal, it is found that process of brittle materials, such as ceramics, its plasticity removal could be done by tiny cutting depth in actual production process.